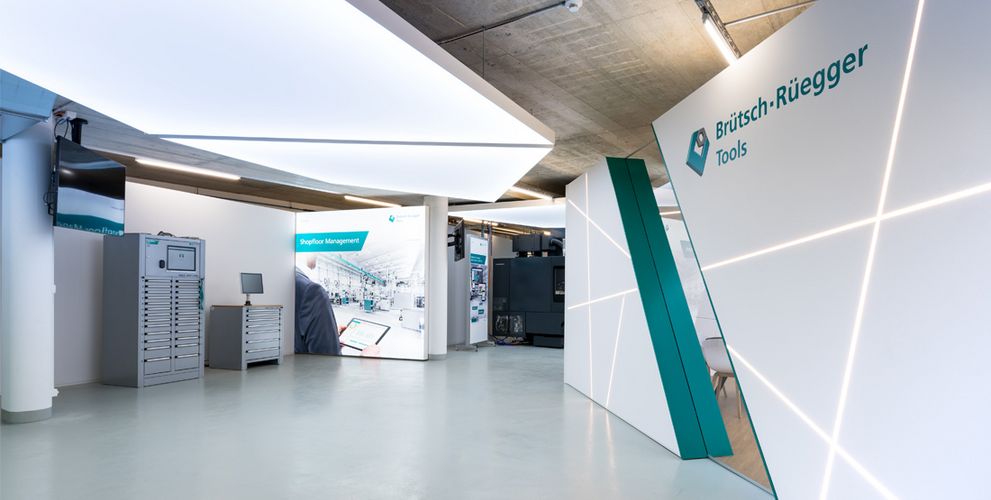
SmartFactory: test, experience, identify and train
Our SmartFactory is made up of a realistic infrastructure and forms a training centre that is able to demonstrate all of the possibilities of Industry 4.0 in a live context. The aim of the training centre is to show visitors a unique implementation of digitalised and networked Industry 4.0 processes. The motto of the factory is "try, experience, identify and train".
In the SmartFactory, all of the processes along the entire value chain have been digitalised and networked with each other. Every single station has been networked with the "Jellix" Industry 4.0 software — from tool management in the ToolBox system and machining optimisation on a five-axis CNC machine, all the way through to the modular and flexible assembly line with reduced throughput times. Information is compared with the target data in real time, the overall plant efficiency is continuously monitored and the entire system is constantly being optimised in line with the principles of lean management.
Topics and content in the SmartFactory:
- Networked systems and processes based on the example of Jellix
- Tool management and tool logistics
- Optimised production: Production planning and machining strategies on five-axis milling machines
- Lean management on assembly and production lines, taking into account discoveries in the fields of ergonomics and workplace design
- Training area for sharing expertise in an interactive format
Virtual tour of the SmartFactory
Tool management and tool logistics
A wide variety of ToolBox systems enable tools and equipment to be managed efficiently. When used as retrieval systems, they guarantee 100% availability thanks to the automatic reordering function. The traceability of cutting tools and measuring equipment is important for auditing and quality assurance purposes, and it provides valuable information for optimising manufacturing processes. What's more, the systems also store the calibration cycles and certificates. The Jellix software links the ToolBox systems with the design and production planning departments and with the machine tools and downstream assembly inspection and quality assurance stations. Experience shows that ToolBox systems reduce the cost of tools and calibration by up to 20% and pay for themselves in less than a year.
Optimised production on CNC machines
Next up: a powerful five-axis milling centre. Machining experts use the machine to demonstrate just how much of an impact the milling strategy, cutting tools, mounting tools, production planning and, above all, the workpiece design have on the quality and processing time. In practice, the right milling strategy can reduce the manufacturing costs of a workpiece by up to 50%. The Jellix software is used throughout the production process and clearly displays all the data you need about the status of production, manufacturing and assembly processes on a smartphone, tablet or other device. Jellix uses the tracking function to pinpoint which stage the workpiece is at in the production process, thereby providing vital information for the optimisation of throughput times.
Assembly line
The next station is a modular assembly line that has been designed with the latest findings in the field of lean management in mind. The facts demonstrated in this area are very impressive: reduction of stocks by 30%, reduction of throughput times by 25% and an increase in value-adding production area while still maintaining maximum flexibility. The lean management expert demonstrates a variety of techniques, from value stream analysis to cyclic assembly and production processes. The tasks that make up the assembly process, such as inspecting and measuring workpieces and screwing processes using torques controlled by the operator assistance system, are all logged automatically. The workplaces are designed in a way that promotes fatigue-free and motivated working, while also ensuring that the entire line can be converted in just a few minutes (modularity for small assembly batches).
Opportunities for further training
The modularity of the SmartFactory and the variety of topics on show mean that it can provide exciting opportunities for further training on tool management and tool logistics, Industry 4.0, digitalisation, optimised production and lean management.
Training sessions, seminars and individual workshops demonstrate to participants the enormous potential of Industry 4.0 practices for SMEs. Cost reductions of 20% across the board and up to 50% in specific areas are very feasible outcomes.
(only in german)