Bone screws – Burr-free right off the CNC swiss type lathe
Reliable deburring process using a diamond brush with 35 % shorter processing time and elimination of downstream work steps.In medical technology, high quality is essential. Standards are strictly and precisely defined. For example, many medical products require at least one visual inspection to ensure long-term precision.
A practical example shows that a state-of-the-art manufacturing concept has the potential to optimise and partially eliminate existing processes and significantly increase quality. This saves time and costs.
Plain lathes have long been a key tool in the manufacturing of bone screws (rotating small parts). Turning, reaming, drilling, chamfering, milling, thread cutting, whirling and shaping are common operations carried out on plain lathes, but the possibilities do not end there.
Brütsch/Rüegger Tools and Zeintra have developed an innovative solution for a leading Swiss contract manufacturer in the medical technology industry and manufacturer of bone screws. The products that will be manufactured will arrive from the plain lathe free from burrs.
The result: The effective processing time was reduced by 35 %!
Benefits at a glance
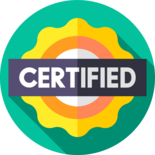
Trust in certified reliability
Diamond brushes validated for medical technology ensure reliability and quality for demanding projects.
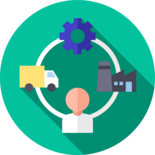
Smooth processes, first-class results
Experience high levels of efficiency and flawless surface finishing, even on difficult materials such as stainless steel and titanium.
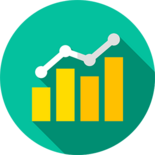
Experienced at providing precision
Benefit from over 110 years of expertise at ZEINTRA for improved performance in CNC applications.
The challenge
During the manufacturing process, a manufacturer of self-tapping bone screws mills the area of the front thread to create a functional cutting edge. The material being processed (titanium or stainless steel) tends to form burrs, which in turn leads to unclean transitions. This results in complex downstream processes such as barrel finishing, which takes extra time and increases costs.
The aim of the project was to ensure that bone screws arrive from the plain lathe ready to use and free from burrs. Non-contact measurement is performed on these orthopaedic products (implants) using an optical measuring system at the machine workstation itself.
The solution
In the scenario described, the bone screw was deburred while on the plain lathe in a single clamping operation, allowing us to produce a burr-free bone screw. We used a Zeintra smartcel diamond brush with an innovative brush filament (bristles). During the manufacturing process of the filaments, ingredients (e.g. diamond or ceramic powder) can be homogeneously incorporated into the eco-friendly bristle filament.
The diamond brushes are already used by a range of manufacturers of medical products and have therefore been validated several times in the field of medical technology.
ZEINTRA diamond brush in use on a CNC plain lathe
The result
Through eliminating an entire downstream process, it was possible to simplify logistics and reduce the effective processing time by 35 %. In addition, process reliability was increased and the time required was minimised.
Within a few weeks, we were able to complete the tests and manufacture and deliver the Zeintra smartcel diamond brushes. The brushes were validated by the customer and the process was implemented in production.
Value-added Services
Customers can contact the "Medical technology" account team at Brütsch/Rüegger Tools at any time if they are facing any challenges. The customer receives individual support from qualified specialists that is tailored to their respective needs. The service not only includes industry knowledge, but also close cooperation with our partners, such as Zeintra.
What can we do for you?
Do you place the highest value on quality and functionality in the manufacture of medical components? Take advantage of our know-how and expertise to achieve the highest quality standards. In combination with our knowledge and experience in medical technology, we understand your needs and requirements very precisely. This enables us to provide you with the best possible advice and work with you to develop the best solutions.